Construction data is hard, and not as simple as do-re-mi (last Jackson 5 reference I promise). Sites and projects are complex, prone to going over budget and creeping out of scope. This makes it hard to understand which materials have gone into a building and where they came from. But why does this matter?
One reason is the UK’s Golden Thread, as part of the Building Safety Bill passed after the Grenfell Tower fire. This necessitates an audit showing every material that went into a building. Another reason is carbon budgeting. Countries are starting to regulate how much carbon can go into a building, and also how much carbon a building can emit. These carbon budgets force developers to care about their data. If you have to work within a carbon budget, you need to know how much carbon your building will use.
Enter LCAs and EPDs. These two acronyms are taking construction by storm.
The regulatory picture
Regulation is the key driver behind the need for tracking building carbon. When I use the term building carbon, I’m referring to „whole life carbon“. This is the sum of embodied carbon, operational carbon, and end-of-life carbon. The figure below gives a good overview of these different types. Embodied and operational carbon are the important ones for us. Embodied carbon in buildings makes up 11% of all greenhouse gas emissions [1]. Operational makes up 26%. Considering how high these sectors are, we’d expect a concerted global effort to reduce them both.
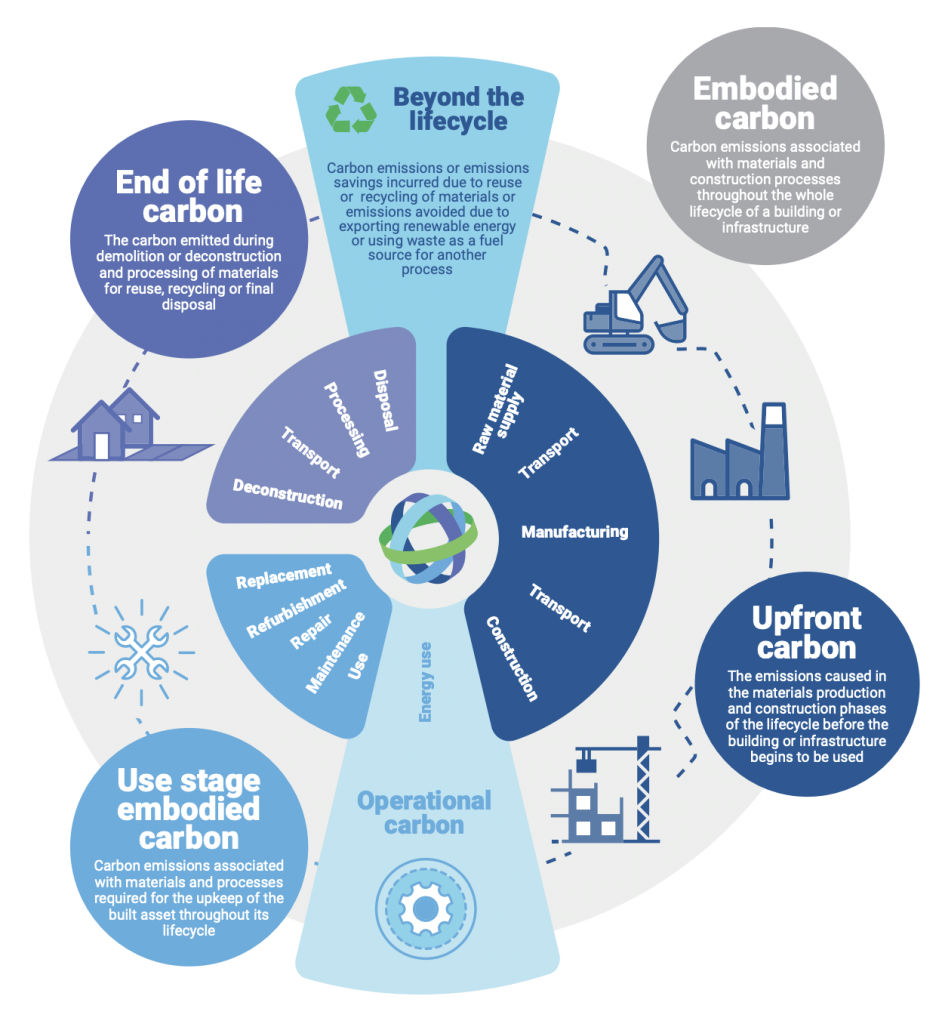
Showing the different kinds of carbon throughout the lifecycle of a building [1]
And so typically, there’s nothing. The EU has taken a stance on this, with the Energy Performance of Buildings Directive (EPBD) [2]. However this only focuses on operational carbon. Future EPBD versions are under negotiation, with pressure to include whole life carbon. The US is no better. There are no federal regulations on whole life building carbon.
Luckily, some European nations and US states are taking action on this. California, Maryland, Colorado, Minnesota, and Oregon have legislated to incentivise materials with low embodied carbon [3]. Additionally, other states have introduced incentives to promote low-carbon products.
Looking across the Atlantic, I think France is one of the best countries in this space. Their National Low-Carbon Strategy (SNBC) defines carbon budgets for different sectors. The budget for “Manufacturing & Construction” for 2019 – 2021 was 75 MT CO2e per year (million tonnes of CO2 equivalent). The actual was 77 MT CO2e [4]. France also has their RE2020 regulation. This came into force in January 2022 and prioritises using low-carbon construction materials [5].
Cities are taking action too, using their control over planning applications and local zoning. For example, London has rejected planning applications due to concerns over high embodied carbon.
Ultimately, there are a few different regulatory pathways:
- Performance Standards: Specific requirements that new construction must meet, such as limits on embodied carbon emissions. Example: the Netherlands‘ MPG (Environment Performance of Buildings) calculation [6].
- Mandatory Reporting and Disclosure: Companies and sectors must calculate and report their environmental impact. Example: Sweden’s Climate Disclosure Act for new buildings [6].
- Lifecycle Analysis Requirements: new buildings must have a life cycle assessment as part of planning . Example: Denmark’s new building codes [7].
- Material and Construction Method Regulations: Developers must use low-carbon and sustainable virgin materials, or reuse and recycle materials in a circular approach. Examples: France’s RE2020, California’s CALGreen [3], and Finland’s Building Act [8].
- Carbon Budgets and Caps: Capping the total amount of greenhouse gases that can be emitted over a specific period. Example: the UK’s Climate Change Act.
- Incentives and Subsidies: Using incentives, subsidies, and tax breaks to encourage adopting sustainable practices and technologies. Example: Toronto City Council [9].
This is a quick overview – my colleague Ada is preparing an overview of whole life carbon regulations. If you’d like to find out more about this please contact her at ada@pt1-x4esqo78i0.live-website.com.
Life-cycle assessments, how they work and where they go wrong
The different regulatory mechanisms above have some things in common. Many of them require some form of whole life carbon reporting. This is an either an explicit requirement (eg Denmark’s specific mandate), or a needed component (the UK’s scheme needs whole life data). So how do we work out the whole-life carbon of a building? The answer is a life cycle assessment (LCA).
LCAs are a standard assessment process showing the total environmental impact of something. This process is formally defined as part of ISO 14000, where it is described as:
LCA studies the environmental aspects and potential impacts throughout a product’s life cycle (i.e., cradle-to-grave) from raw materials acquisition through production, use and disposal. The general categories of environmental impacts needing consideration include resource use, human health, and ecological consequences.
Here’s a very basic example of how you can do an LCA. I’m making a building. I have a bill of materials, which is the „ingredients“ for my building. For each material, I find its carbon intensity. This is also called the global warming potential (GWP). The GWP is measured in tonnes of CO2e, per unit. For example, some insulation has a GWP of 5kg CO2e/ sqm. Producing one square metre of this insulation emits 5kg CO2e. I could find this value from a material database, or the producer might have given it to me. Then, I would look up how much of this material I’m using from my bill of material (say 300 square metres). After that, I’d work out the total GWP for this material: 300sqm x 5kg CO2e/ sqm = 1,500kg CO2e. A proper LCA would also take into account how far the material travelled to get to me, and the emissions of any on-site processes.
To get the final LCA, repeat this for every single material in the building. This would give us a “process LCA”, as we follow the construction process to get there. This is a simplified example, but even in this case the complexity of an LCA is clear. Producing an actual building LCA is not easy. Thankfully, there are some startups in this space to make things easier.
A full market map on relevant startups is far beyond the scope of this article. But at a high level, we have the following segments:
- Materials databases: these solutions provide information on construction materials. This allows easy benchmarks (for LCA calculations), but also lets developers compare products. These tools are moving towards lead generation platforms or marketplaces for construction.
- Planning and design: these tools bring embodied carbon checks to the planning stage. Architects can course correct while in the design stage. These tools are most useful when the project is at RIBA Stage 2. (RIBA’s plan of work is a great framework to classify ConTech startups – it’s worth checking it out here.)
- Report generators: these generate the necessary reports: LCAs, EPDs), or ad hoc.
- Construction auditors: tracking the actual embodied carbon, during construction.
There are a lot of startups in these segments. I’ve spoken to many of them myself. The forerunner in this space, and arguably no longer a startup, is One Click LCA. As the name suggests, they make LCA production easier and faster. They also claim to have the world’s largest construction material database. Starting in 2001 as LCA consultants, One Click LCA has since dominated the market. They made headlines recently, raising a €40m round for strategic growth. Many of these startups have grown in response to the growth in LCAs and the complexity of producing them.
However, LCAs aren’t perfect. Recently there has been one major problem with building LCAs: their comparability. LCAs for similar buildings have hugely different results. This raises doubts about the reliability of LCA data.
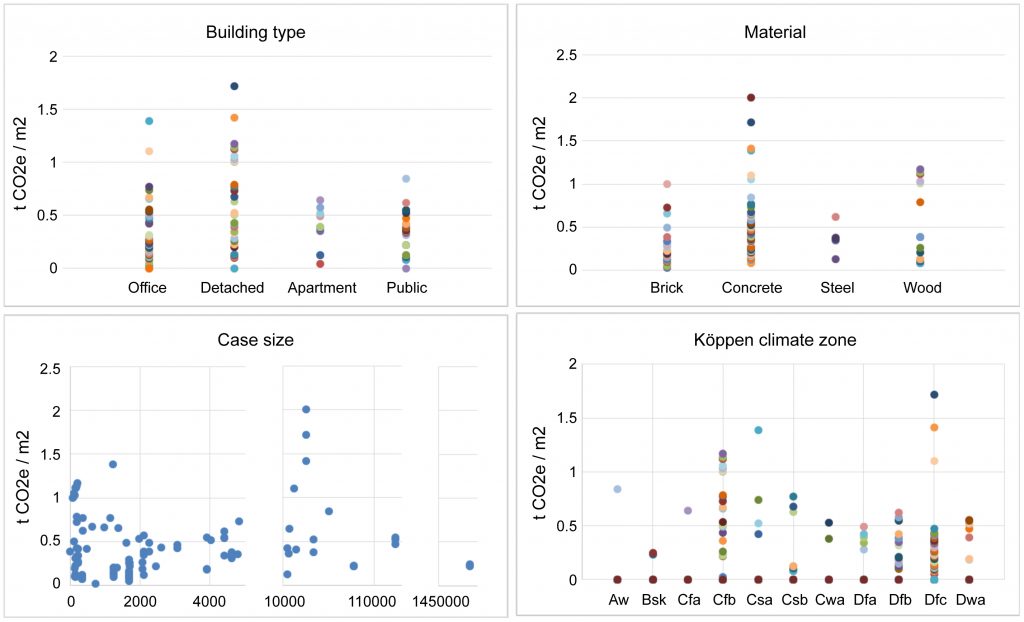
These graphs [10] show the GWP of from some LCAs for different buildings. We see a huge distribution in GWP per square metre for the same building type. There’s a max variance of 2 tonnes CO2e per sqm, which adds up quickly. Two different consultants analysing London’s Gherkin could produce LCAs with a total GWP difference of 130 million kg CO2e.

Underestimating is dangerous – we’d end up blowing way past our carbon budgets. Overestimating is just as dangerous. It stifles new development, by mislabelling projects “too” carbon intensive.
Some inaccuracies are due to different methodologies, but there are also inter-methodology problems. Comparing GWPs shows us that one method (input-output LCAs) leads to consistently higher results than from other methods [11]. This makes it hard for policy-makers to engage with LCAs. This is an inherent flaw: a layperson can’t compare LCAs without understanding the different methods.
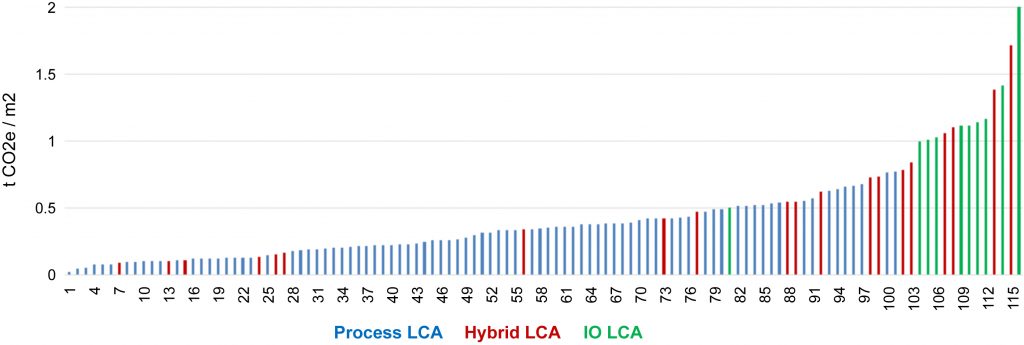
LCAs also have loads of data points, and this abundance of data can lead to information overload. A common recommendation is to simplify LCAs to a single indicator. For example we’d just focus on GWP and ignore all the other metrics. But even this isn’t perfect. Different countries have different LCA guidelines. Identical office buildings, on either side of the Danish-Swedish border, have different GWPs. The Danish building has 2.5x more global warming potential – for the exact same building [12].
We are living in a material world
There’s one other problem we’re yet to discuss. LCAs are calculated using material data. But where does this data come from? And how accurate is it?
There are several online material databases, which provide benchmarks for different materials. We can use these, ie the median GWP for steel framing. The issue is that not all materials are created equally. I looked at a few example materials, using the Carbon Leadership Forum’s 2021 baseline data [13].
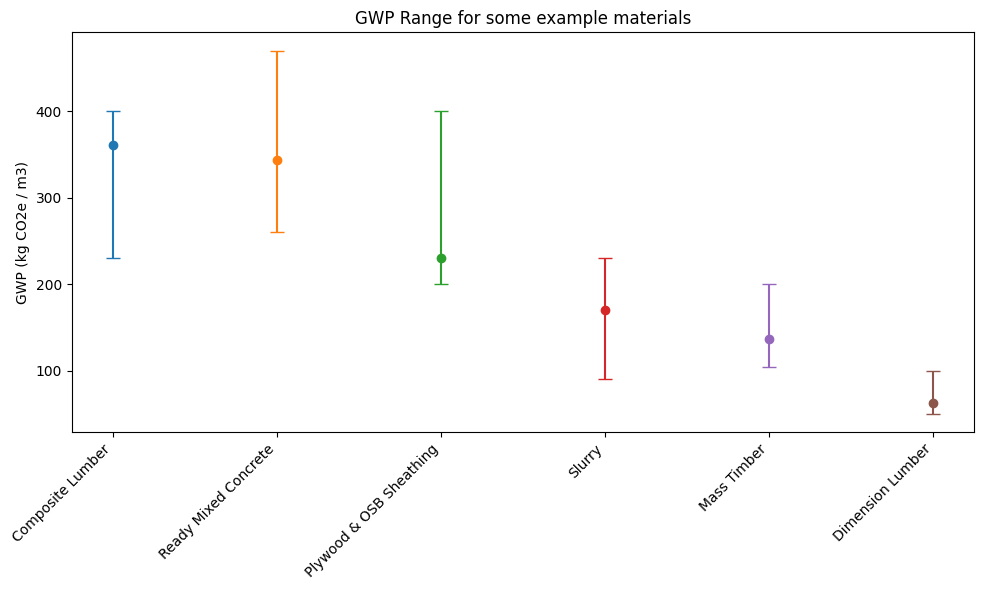
They collate the different kinds of composite lumber (for example), and provide the median, top (80th percentile) value, and bottom (20th percentile) value. I compared 6 examples from the data. For composite lumber, the top value is almost double the bottom. Herein lies the problem. LCA calculations are susceptible to this huge variation. Say I’m building a construction project, and I’m using Composite Lumber. My LCA consultant would use the benchmark (median) value in their calculations. If I decide to use the worst material there’ll be a huge difference between the LCA value vs the actual value. My LCA would heavily underestimate my carbon impact.
Environmental Product Declarations (EPDs) are one way to fix this. Rather than rely on material benchmarks, each material supplier creates product specific EPDs. These are also produced following an ISO 14000 mandated process.
The market response to EPDs has been positive. I’ve spoken to several material producers in the space who are producing their own EPDs. EPDs offer them a competitive edge when selling to developers. Rather than use a product without an EPD (where I’d have to rely on the material benchmark), I can use a product with an EPD and reduce my project’s GWP. We’re seeing a growth in the number of EPDs prepared, with an estimated 130,000 EPDs globally. The graph below shows how this number has been growing exponentially in the last ten years [14].
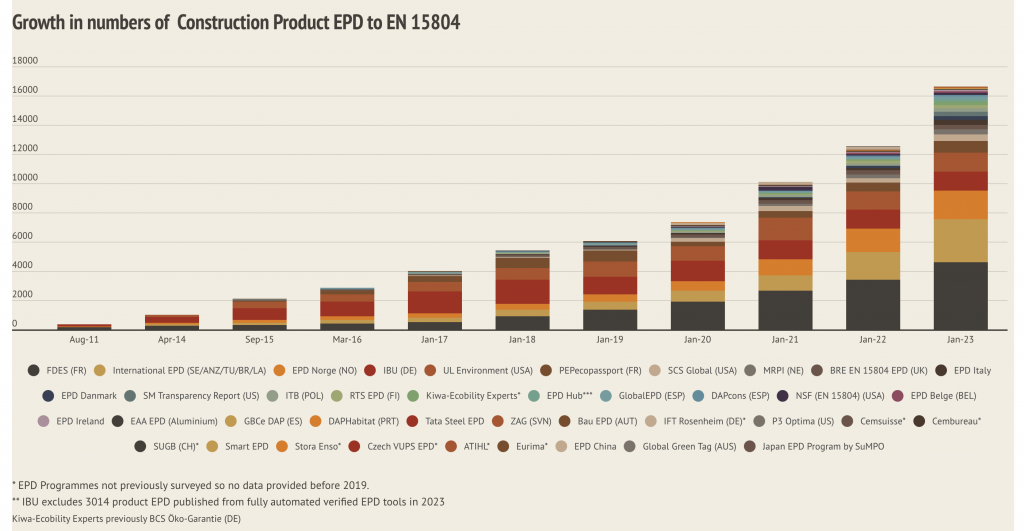
I suspect we’re only scratching the surface with EPDs. 130,000 EPDs isn’t enough to cover every construction product globally. I suspect we’re missing many (in the order of half a million). This gap will need filling if regulation changes.
There’s one key challenge though. EPDs are very detailed. For example, EPDs vary based on the supply chain and where production facilities are. This means a supplier could have two different EPDs for identical products, if they’re made in different places. We can see an example of this below [15]:
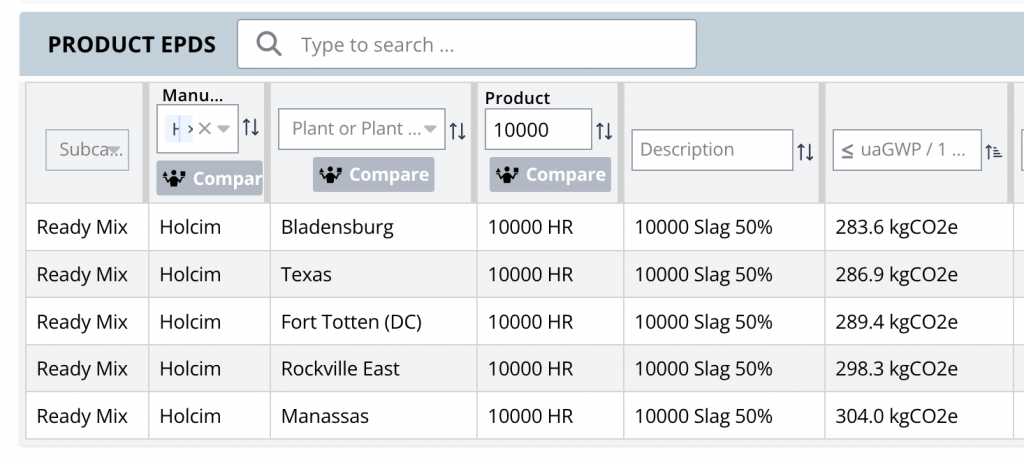
Above we compare EPDs for 5 identical ready mix concretes, all produced by Holcim. The GWP (rightmost column) varies for each of them, with Bladensburg being the most environmentally friendly. The fact that there’s a difference is a testament to how much data is needed to create an EPD. These are complex calculations, needed for hundreds of thousands of products. They must also be updated whenever there’s a significant supply chain or process change. I spoke to a large European product manufacturer about this. They’ve spent a year building internal tooling to help with EPD generation. Creating EPDs across an entire product portfolio is complex. The complexity increases with the number of products and with the components in each product. I spoke to another major European manufacturer, and they are actively looking for software providers to help them produce and manage their EPDs.
We’ve seen a few early-stage startups in this space. In New York, Pathways recently raised €2.5m to build out their AI-powered EPD generation software. Their investors included Zacua Ventures, a ConTech expert, as well as Pi Labs, the UK’s oldest PropTech/ ConTech VC.
Speaking to Mauricio Tessi Weiss, a Founding Partner at Zacua Ventures, about his view on this space:
„Creating an EPD in the construction industry is a complex and resource-intensive process, depending on the type of product and the available data: it requires expertise in LCA methodology, manual data collection, formatting, and organization, collaboration with suppliers and manufacturers to access relevant data, and the use of LCA software. This process takes 7-12 months and is often outsourced to expensive consultants. An EPD and LCA is often created using 12 months of historical data, and so by the time a process is complete, the data can already be outdated or there have been changes in the material supply chain.
This process is an excellent use case for AI automation to save human time: Solutions that can integrate directly into supplier databases, or even automatically extract information from PDFs or Excel spreadsheets save us from tedious copy+paste (or paying consultants to do it!) and prevent the need for manual data entry. A faster and more automatic LCA process allows for more real-time modelling into the supply chain, where suppliers can test out the purchase or inclusion of new materials and see how this changes carbon, price, and time.“
In Europe, Emidat is the earliest startup I know of who are generating EPDs. Vizcab, a French startup who recently raised a €5m Series A are also in this space. Vizcab started out with a solution to help French construction companies comply with RE2020 legislation, but working on EPD generation is a logical next step. Vizcab’s Series A was led by KOMPAS VC, another ConTech expert, and also included A/O PropTech, Europe’s largest built world VC. Specialist VCs are clearly starting to converge on this sector. But what about the Finnish sleeping dragon?. One Click LCA also offer automated EPD generation to their clients. Can these newer startups outmanoeuvre One Click LCA’s 20+ year legacy codebase? Or will One Click’s €40m war-chest allow them to buy or build their way to success?
In my opinion, the advent of large language models and the availability of material databases are the building blocks for EPD generation. The market still has some concerns though. I spoke to someone responsible for tech procurement at a large European general contractor. They were concerned about the liability and damages from incorrect LCAs from bad EPDs. Their worst case scenario would be the following:
- they start construction on a project, and choose a particular product based on its EPD (eg steel framing)
- their project’s total GWP complies with relevant carbon budget regulations
- after construction, they realise there was a mistake in the auto generated EPD
- the project has now completely exceeded its carbon budget
- who’s on the hook for fixing this?
These problems are surmountable, but I can empathise with these concerns. Would any startups really want to be liable for the quality of their AI generated EPDs? We’ve seen enough issues in LLMs to be wary. And if the startup refuses liability, will material producers feel comfortable with this?
EPDs are a good thing. They bring clarity and transparency to a previously opaque area. There’s also potential for huge greenhouse gas savings: all though decreasing embodied carbon. But, the value chains are complex (startups -> material producers -> contractors -> architects -> owners). The regulatory framework is fragmented. And things are changing quickly.
My predictions for the future
What does this mean for the built environment? Here are my predictions and what I’d like to see:
- The zeroth axiom, upon which all my predictions rest, is that we’ll see more regulation to decrease embodied carbon. The mechanism doesn’t matter. What’s key is that this regulation will introduce a need to report on embodied carbon.
- This grows the market for tools like One Click LCA, Vizcab and others. There are many solutions, all focusing on different parts of the value chain. I expect to see consolidation. I also suspect players like Autodesk or the Nemetschek group will begin to move in here. Integration is one approach, and acquisition is the other.
- I’d like to see European and US level consolidation for LCA methodology. This could be mandated top-down, or arise organically with the market picking a preferred approach. This will reduce some of the comparability problems we saw with LCAs earlier.
- EPDs will become more common, bringing LCA usage away from material databases. I’m curious what some material database startups will do. Will they pivot into EPD databases, or become something else? Kompozite, a French startup, has already done this. They previously had a building materials database. They have since shuttered this and are now tracking Scope 3 for construction.
- EPDs will offer material producers a competitive edge. If I were a developer, trying to meet a carbon budget, I’d pick the product with the lowest reportable GWP. The keyword here is reportable. ACME Ltd could produce a type of concrete that is 5x lower than the benchmark. But without an EPD, why would I use it? ACME’s „wundercement“ may be 5x lower than the benchmark, but without an EPD I can only report the benchmark. The product might be better in real life, but without an EPD it’s not attractive. This market demand will fuel the need for EPD generative software. I’m really intrigued by the unit economics of these companies. Is there sufficient value in just generating EPDs? Or will these startups expand to become a marketplace and lead generation tool for their clients, linking material producers to potential customers?
- These LCAs and EPDs are pre-construction. We need to make sure the constructed building meets the forecast carbon budget. This requires checks during construction (to course-correct) but also an audit post construction. There are good startups enabling these course-corrections. But what about the post construction audit? Tech platforms used by the developer won’t be enough. I’d like to see 3rd party audits and carbon assessments. Ideally these would be legally mandated. However we lack the skilled workforce to do this en-masse. We know there’s a surge in EdTech startups helping build the skilled workforce for the transition to Net Zero. Our portfolio company Greenworkx is one of them, and Sifted published a piece last week on this topic. Could this be the start of a new labour shortage?
This is an interesting space, and it fits neatly into several megatrends. It’s also one I’ve been watching for some time. We’ve not made an investment into this space yet, but we have spoken to many of the startups mentioned above (as well as many others not mentioned). These LCA and EPD processes have always been very text heavy, and existing examples are full of unstructured data. Advances in LLM have sparked this paradigm shift we’re seeing: now tech can produce the necessary paragraphs and learn from the existing ones. As always, if you’re building in this space or would like to discuss further – please reach out to burhan@pt1-x4esqo78i0.live-website.com
Sources:
- World Green Building Council, “Bringing Embodied Carbon Upfront”, https://worldgbc.s3.eu-west-2.amazonaws.com/wp-content/uploads/2022/09/22123951/WorldGBC_Bringing_Embodied_Carbon_Upfront.pdf
- https://www.euractiv.com/section/energy/opinion/embodied-carbon-addressing-now-the-hidden-carbon-cost-of-our-buildings/
- https://carbonleadershipforum.org/tangible-next-era-building-codes/
- https://www.statistiques.developpement-durable.gouv.fr/edition-numerique/chiffres-cles-du-climat-decembre-2022/en/23-state-policies-to-combat-climate
- https://www.agora-energiewende.org/international/success-stories/reducing-embodied-carbon-in-construction-materials-re2020-in-france-1#:~:text=Reducing embodied carbon in construction materials%3A RE2020 in France,-Region%3A France&text=In France%2C up to 90,a cap on those emissions.
- https://www.preoptima.com/the-carbon-source/embodied-carbon-regulations
- https://vbn.aau.dk/ws/portalfiles/portal/545269068/sustainability-15-10992.pdf
- https://valtioneuvosto.fi/en/-/1410903/parliament-adopted-acts-that-will-reduce-emissions-from-building-and-promote-digitalisation
- https://mantledev.com/insights/toronto-becomes-first-jurisdiction-in-north-america-to-enact-whole-building-embodied-carbon-caps-on-new-city-owned-buildings/
- Antti Säynäjoki et al 2017 Environ. Res. Lett. 12 013001
- https://www.tandfonline.com/doi/full/10.1080/09613218.2023.2236254
- https://2050-materials.com/blog/comparing-differences-in-building-life-cycle-assessment-methodologies/
- https://carbonleadershipforum.org/2021-material-baseline-report/, graph created by PT1
- https://bit.ly/2023-EPD., graph and data from Jane Anderson, ConstructionLCA
- https://buildingtransparency.org/ec3/material-search, data extracted on 18th March 2024